

Once the artwork to be screen printed has been selected and prepared, it is time to gather the rest of the necessary materials and equipment. Gather the Materials Needed for Screen Printing Whether it is printed or hand-drawn, the artwork blocks the emulsion on the screen and the emulsion is washed off the design, allowing the ink to pass through the screen and transfer the design onto the T-shirt or other object that is imprinted.Ģ. The objective is to create what artists call a “film positive” of the artwork, which is 100 percent black on a clear background. Beginners should create simple designs with fairly clear, thick lines since screen printing delicate, fine-lined artwork can be tricky. Original artwork can be painted directly onto a transparency or onto any piece of sturdy, clear plastic. Most copy shops do this for a very small fee. The best way to prepare artwork to be screen printed is to have it copied onto a transparency. Choose or Create the Artwork to Be Screen Printed If you’re looking into printing a completely different image, make sure to buy an emulsion remover to get the screen clean and use the frame/fabric again.The process of screen printing using mesh stencils made with photosensitive chemical emulsions are explained below, with helpful tips for each step to enable any artist (whether novice or expert) to achieve success in screen printing.ġ. Ink drys really fast and will be a real pain to get off once it does. To finish, lift up your screen, pull the cardboard out slowly, then you're done!ĭIY tip: If you want the image to stick, place it in the oven at 400 degrees Fahrenheit for about half a minute.Īs soon as you’re done printing, wash the ink off your equipment. Move the squeegee up and around ever direction carefully, and right a couple times to push all the ink through onto the shirt. For the all the first-timers, you should practice on paper before you do this on a shirt. Next, take your squeegee and make one smooth move across the screen with a lot of pressure.
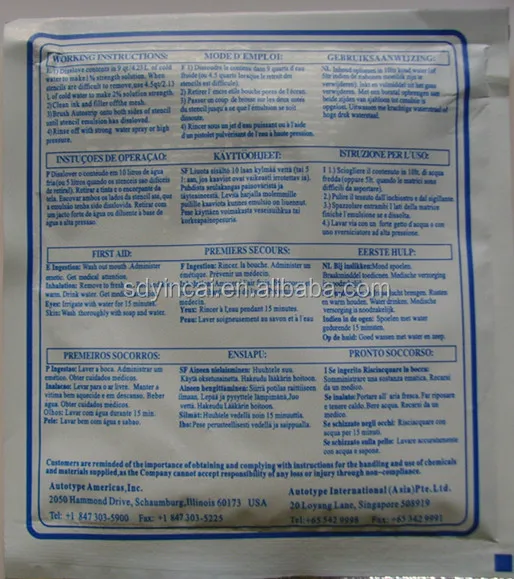
Place the screen over the shirt with your design in the area you want to print it.Ĭarefully pour a small portion of ink across your screen horizontally. Once it’s dry, you’ll want to cover any exposed portions of the screen (areas with no photo emulsion) with tape.įind a flat surface to place your shirt, then place the piece of cardboard underneath the area that you want to print. When you’re done, hold your screen up to the light to see if it’s just like the transparency.

To clean the screen, spray it down with cold water (shower heads & hoses work fine) Keep spraying until you can see completely through your image. Once you’ve decided on your final image, print it on to transparency paper. Your image will later be burnt into an emulsion. You’ll need the solid black so you can block the light. Stick with a simple solid black image with minimal detail. To start, don’t do anything too complicated. Piece of cardboard (Fits inside the shirt). Screen/frame, which you can buy at local arts stores or purchase a set like this for just $14. To start you DIY silk screen print shop, you will need these items, minimum: Instead of cut-outs you create a photo emulsion, then create a cutout of the image using bright lights. Similar to stencils, silk screen printing is a simple concept once you got it down. Screen printing can be intimidating at first, but with just a little bit of time and extra cash, you can have your personally functional print shop!
